The Complete Guide to Sand Making Machine Maintenance: Ensuring Long Life and Peak Performance
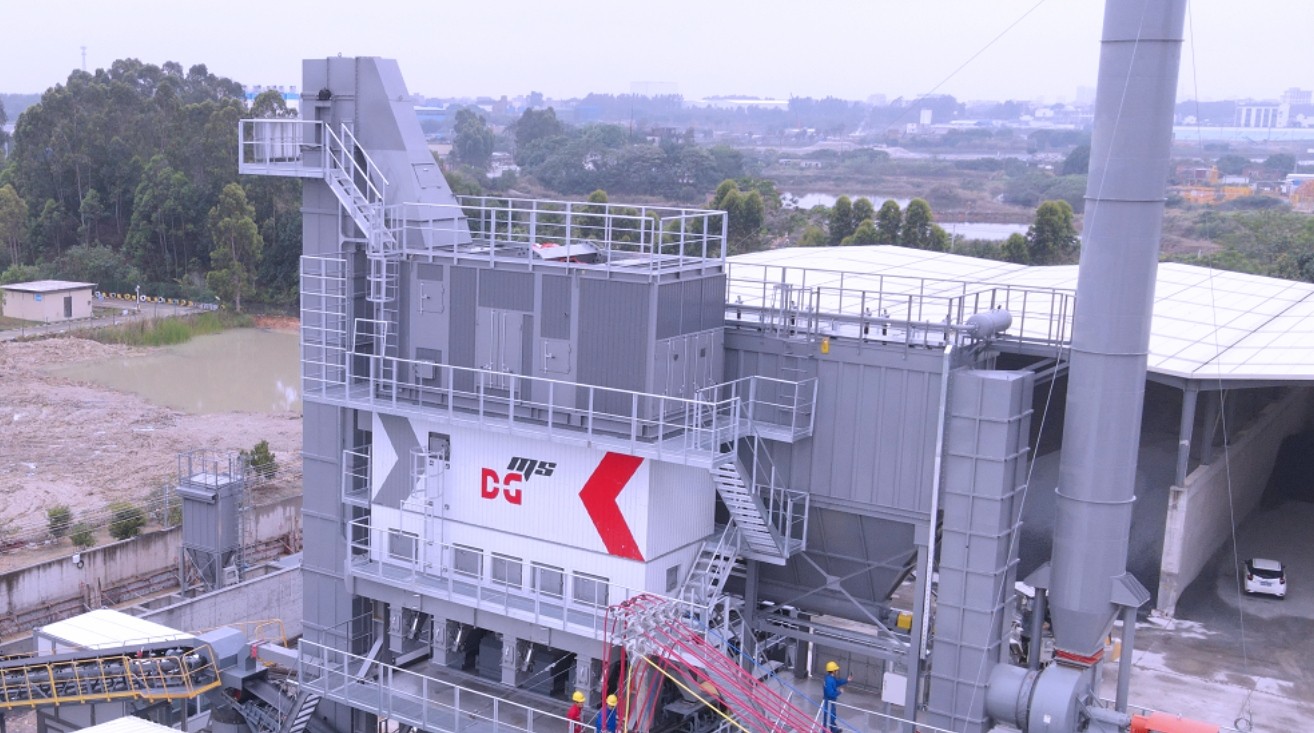
Sand-making machines are indispensable tools in the construction industry for the production of sand and aggregate for various purposes. The working environment of the sand-making machine is generally harsh environment, coupled with the long-term continuous operation; it is likely to cause the failure of the sand-processing equipment. Regular maintenance is essential to ensure the longevity and peak performance of these machines. In this article, we explore the importance of maintenance, discuss sand-making machine maintenance tips, outline safety precautions, and provide a troubleshooting guide for sand-making machine owners.
Why Should Sand-Making Machines Be Maintained?
Maintaining your sand manufacturing machine is critical for a number of reasons. By implementing regular maintenance practices, you can:
Preventing Failures: Regular maintenance helps identify and resolve potential problems before they escalate into major failures. This proactive approach minimizes unplanned downtime.
Optimized Productivity: Well-maintained machines run at peak efficiency, increasing productivity. Regular inspections and maintenance keep your sand-making machine running smoothly, delivering consistent output and quality.
Extended Service Life: Proper maintenance can significantly extend the life of your sand-making machine. By maintaining your equipment and addressing wear and tear, you can avoid premature failure and costly replacements.
Ensuring Safety: Maintenance practices not only improve machine performance, they also enhance safety. Regular inspections help identify potential safety hazards, such as loose parts or failed components, reducing the risk of accidents for operators and other workers.
Cost Savings: Investing in maintenance is a cost-saving measure in the long run. By catching and fixing problems early, you can avoid costly repairs or replacements. Plus, well-maintained machines use less energy and have lower operating costs.
Maintain Quality: A properly maintained sand processing equipment ensures consistent product quality. Regular cleaning, lubrication, and replacement of components help maintain the efficiency of the machine, which produces high-quality sand and aggregate for construction purposes.
How Do D&G MACHINERY Help Customers Maintain and Operate Sand-Making Machines?
The following are the methods and steps that D&G MACHINERY helps customers maintain and operate sand making machines effectively.
1. Close the sand making machine regularly, open the observation door to observe the internal wear of the machine, check the wear degree of the cone cap, the upper and lower flow channel liners of the impeller, the peripheral guard plate, and the wear-resistant block, and replace or repair them in time, and replace the wear-resistant The blocks should be replaced at the same time to ensure the same weight of the wear blocks. It is strictly forbidden to open the observation door to observe the internal working conditions during the working process of the sand making machine, so as to avoid danger. If the impeller body is found to be worn, replace it in time or find the manufacturer to repair it.
2. The sand manufacturing machine uses Mobil special-grade grease or lithium-based grease. Add appropriate amount of grease every 400 hours of work, open the spindle assembly to clean the bearing after 2000 hours of work, and replace the new bearing after 7200 hours of work.
3. The tension force of the transmission triangular belt should be adjusted properly to ensure that the triangular belt is evenly stressed. When the double motor is driven, the triangular belts on both sides should be selected in groups to ensure that the length of each group is as consistent as possible, and the current difference between the two motors should be adjusted in time. The current difference of the two motors should not exceed 15A.
4. The sand making machine equipment is a high-speed equipment. During the operation of the sand making machine, special attention should be paid to safe production. The relevant personnel should stay away from the equipment. If the equipment needs to be repaired, the operation should be carried out after the power is turned off and shut down.
5. Before starting the sand processing equipment, you must check whether the observation door of the crushing chamber is closed tightly to prevent the material from rushing out during operation, and check whether the rotation direction of the impeller is correct. The impeller should rotate counterclockwise when viewed from the direction of the material inlet.
6. The start and shutdown sequence of the sand making machine also meet the requirements of the specification, the material must be discharged first, and then feed, the sand making machine needs to start empty, residual material in the crushing cavity may cause the motor start pressure too high and burn the motor, it can result in other damages to the equipment as well. Therefore, the sundries in the crushing cavity must be cleaned before starting the equipment, start the equipment without load, and then feed the material after the sand making machine is running normally. The stop sequence is opposite to the start sequence.
7. Regularly check and tighten loose parts in time. The sand making machine will loosen under the influence of violent movement during high-speed operation. During use, if there is abnormal noise, it must be stopped immediately for inspection to find out and fix loose parts,.
8. It is strictly forbidden to feed iron during the production process of the sand making machine. Because the sand making machine runs very fast, the impeller flow channel is equipped with a hard alloy cutter head. Once iron is fed in, it will directly damage the cutter head, damage the rotor spindle, or even break the cavity , causing irreparable losses, so one or more iron removal devices must be installed before entering the sand making machine to ensure that no iron would enter the equipment.
What Are the Common Sand Making Machine Failures? How Should It Be Solved?
The followings are some common faults and corresponding solutions during the use of sand-making machines:
1) The swing range of the fuselage is too large
2) Abnormal noise from the equipment
3) The bearing temperature is too high
4) Strain caused by environmental factors
5) The hardness of the material, the particle size of the feed, and the humidity will wear the equipment
Solution
1) The Swing Range of the Fuselage Is Too Large: The swing range of the fuselage for the sand-making machine is too large, indicating that the stone particle size is too large when feeding, and there are obstructions in the impeller flow channel, which leads to the loss of balance in the horizontal direction of the impeller, uneven feeding and oscillation. In this case, it is necessary to stop the machine to check the impeller, remove the blockage in the impeller channel, and clean the impeller and crushing chamber.
2) Abnormal Noise from the Equipment: When the equipment has abnormal noise, stop it immediately and check the equipment. The possible reason is that the internal impeller assembly and wearing parts are loose. It is recommended to tighten the bolts of each part before starting the machine. Check wearing parts. (Reminder: If the sand-making machine emits severe vibration or abnormal noise during operation, it should be stopped immediately to check the problem)
3) The Temperature of the Bearing Is Too High: The temperature of the bearing is too high. Generally, foreign matter such as dust enters the main shaft rotor. It may also be that the bearing part lacks lubricating oil, or the bearing has been damaged due to excessive wear. It is recommended to carry out oiling maintenance on the bearing regularly. According to the operation conditions and operation time, replace the bearings, and clean the bearing parts before use as needed.
4) Strain Caused by Environmental Factors: The working environment of the sand-making machine will also directly affect the service life of the equipment itself. For example, in places where there is wind and sand all year round, it will inevitably lead to sand and dust entering the equipment, and wet areas will cause water to enter the parts of the equipment and thrust. It is recommended to install a dust cover on the device itself for protection.
5) Material Hardness, Feed Particle Size, and Humidity Wear on Equipment: Sand-making machines of different models and structures have different requirements for material hardness, feed particle size, and humidity. If the hardness, material particle size, humidity, and other materials of the material are beyond the use scope of the equipment, it may result in a braised car, blockage, serious wear, and other conditions, causing serious damage to the sand machine. Therefore, we should choose the proper equipment that matches the required specifications of the crushing material.
Safety Instructions When Maintaining Sand-Making Machine
When performing maintenance on your sand-making machine, it is vital that safety be your top priority. Here are some basic safety precautions offered by sand-making machine manufacturer:
Proper Training: Make sure operators and maintenance personnel are properly trained in the safe operation and maintenance of your sand-making machine. This includes understanding the machine's components, operating procedures, and safety regulations.
Lockout/Tagout Procedures: Always follow lockout/tagout procedures before performing any maintenance or repair work. This involves disconnecting the machine from the power source and securing it to prevent accidental startup. Use lockouts and tags to clearly indicate that maintenance is taking place.
Personal Protective Equipment: Wear appropriate PPE such as eye protection, gloves, and hearing protection when working on the machine. PPE helps protect against potential hazards, such as flying debris, chemicals, or excessive noise.
Machine Shutdown: Before starting any maintenance tasks, make sure the machine is completely shut down. Follow the manufacturer's instructions for proper shutdown procedures to avoid any unintended movement or activation of machine components.
Work in a Well-Ventilated Area: If maintenance tasks involve the use of cleaning agents or lubricants, make sure the work area is well-ventilated. This helps prevent the build-up of harmful fumes and ensures a safe working environment.
Avoid Loose Clothing and Jewelry: Remove any loose clothing, jewelry, or accessories that may become caught in moving parts of the machine. Wear clothing that fits well and is appropriate for the task at hand.
Use Proper Tools and Equipment: Always use proper tools and equipment for maintenance tasks. Make sure they are in good shape and well-maintained. Using the right tools can reduce the risk of accidents and increase productivity.
Periodic Inspections: Periodically inspect machine safety features such as emergency stop buttons and safety guards. Any damaged or malfunctioning safety components should be promptly repaired or replaced.
Follow Manufacturer's Guidelines: Follow the manufacturer's recommended maintenance guidelines and schedule. These guidelines provide specific instructions tailored to your sand-making machine model to ensure optimum safety and performance.
By following these safety precautions, you can create a safe working environment for your maintenance personnel and minimize the risk of accidents or injuries during sand-making machine maintenance. Before the sand-making machine is put into production, D&G MACHINERY will conduct professional training for the operation and maintenance personnel to ensure the safe and efficient production of the sand-making machine.
In Conclusion
Regular maintenance is essential for smooth operation, service life, and optimized performance of your sand-making machine. By following basic maintenance practices, employing advanced technology, adhering to safety precautions, and promptly addressing common problems, you can ensure machine reliability and produce high-quality sand and gravel aggregate for construction projects. Remember that maintenance is an investment that increases productivity, reduces downtime, and saves money in the long run.