China's Premium Asphalt Plant Manufacturer | D&G Machinery Stock Code 1301.HK | Completely Road Construction Solutions Provider, Pursuing Excellence
How to reduce energy consumption in asphalt mixing plant?
Asphalt mixing plant is a key equipment in road construction. Although widely used in road construction, it consumes a lot of energy and has pollution such as noise, dust and asphalt fume, calling for treatment to save energy and reduce consumption. This article analyzes the factors related to energy saving of asphalt mixing plant including cold aggregate and combustion control, burner maintenance, insulation, variable frequency technology, and proposes effective measures for energy conservation.
a) Aggregate moisture content and particle size
- Wet and cold aggregates must be dried and heated by the drying system. For every 1% increase in wet and cold degree, energy consumption increases by 10%.
- Prepare slopes, concrete hardened floors, and rain shelters to reduce the moisture content of stone.
- Control the particle size within 2.36mm, classify and process aggreates of different particle sizes, and reduce the workload of the drying system.
b) Fuel selection
- Use liquid fuels such as heavy oil, which has low water content, few impurities, and high calorific value.
- Heavy oil is an economical and practical choice because of its high viscosity, low volatility, and stable combustion.
- Consider the purity, moisture, combustion efficiency, viscosity, and transportation to select the best fuel.
c) Combustion system modification
- Add heavy oil tanks and optimize the fuel feeding part, such as using pneumatic three-way valves to automatically switch between heavy oil and diesel oil.
- Carry out system modification to cut energy consumption and improve combustion efficiency.
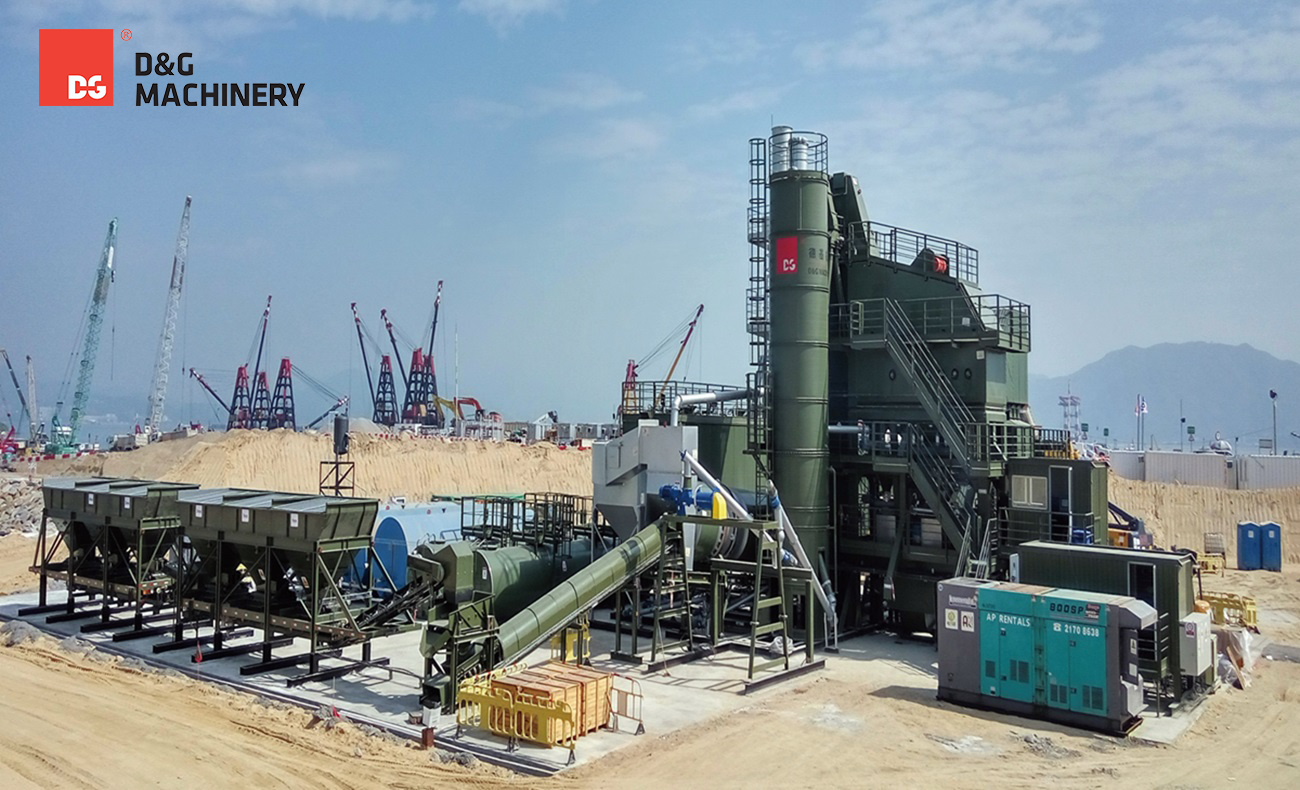
2. Burner maintenance
a) Maintain the best air-oil ratio
- According to the characteristics of the burner and production requirements, adjust the feeding ratio of air to fuel to guarantee combustion efficiency.
- Check the air-oil ratio regularly and maintain the optimal condition by adjusting the air and oil supply systems.
b) Fuel atomization control
- Select a suitable fuel atomizer to ensure that the fuel is fully atomized and improve combustion efficiency.
- Check the atomizer status regularly and clean the blocked or damaged atomizer in time.
c) Combustion flame shape adjustment
- Adjust the position of the flame baffle so that the center of the flame is located in the center of the dryer drum and the flame length is moderate.
- The flame should be evenly distributed, not touching the wall of the dryer drum, with no abnormal noise or jumping.
- According to the production situation, properly adjust the distance between the flame baffle and the spray gun head to obtain the best flame shape.
3. Other energy-saving measures
a) Insulation treatment
- Bitumen tanks, hot mix storge bins and pipelines should be equipped with insulation layers, usually 5~10cm insulation cotton combined with skin covering. The insulation layer needs to be checked and repaired regularly to ensure that heat is not lost.
- The heat loss on the surface of the dryer drum is about 5%-10%. Insulation materials such as 5cm thick insulation cotton can be wrapped around the drum to effectively reduce heat loss.
b) Application of frequency conversion technology
- Hot mix conveying system
When the winch drives the conveying system, the frequency conversion technology can be used to adjust the motor frequency from the starting low frequency to the transportation high frequency and then to the braking low frequency to cut energy consumption.
- Exhaust fan motor
The exhaust fan motor consumes a lot of power. After the introduction of frequency conversion technology, it can be converted from high to low frequency as per demand to save electricity.
- Bitumen circulating pump
The bitumen circulating pump works at full load during mixing, but not during recharging. Frequency conversion technology can adjust the frequency according to the working status to reduce wear and energy consumption.
To sum up, the high energy consumption of asphalt mixing plants goes against the trend of energy conservation and emission reduction. Cold aggregate combustion control, dryer drum insulation and frequency conversion technology can be implemented to effectively control energy consumption, promote comprehensive energy conservation of the system, improve economic and social benefits, and thereby enhance the competitiveness of the plant. D&G Machinery provides you with various upgrading solutions for energy saving. For details, please do not hesitate to contact us.