Digital Intelligence Interconnection, AI for the Future ——D&G Machinery’s “DG Reach Service System”Embraces Big Data to Boost Accuracy
Since its establishment in 1999, D&G Machinery has been committed to building a national brand, breaking the situation that China's high-end equipment mainly relied on imports. To date, over 800 asphalt mixing plants have been sold worldwide, with products distributed across all provinces, cities, and autonomous regions in China, and exported to more than 40 countries and regions, including Russia and Australia. As early as 2006, D&G Machinery realized the challenges of remote overseas locations and insufficient service network coverage, which often resulted in customers' plant issues not being resolved promptly. For example, for customers in Australia, India, domestic engineers needed to spend several days to reach the job site, which not only lowered the equipment's usage efficiency but also hindered the progress of on-site construction.
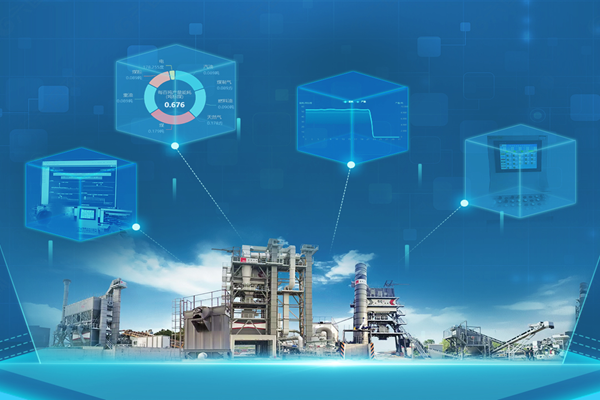
Facing the increasingly fierce competition of traditional construction machinery with severe homogenization, D&G Machinery has taken the lead in introducing "big data" technology into the traditional construction machinery industry and developed the DG Reach Service System. By remotely collecting operation data of the equipment, key parameters such as current, voltage, and temperature during operation are feedbacked to the backend in real time. With years of experience and accumulated data in the asphalt mixing plant industry, it has achieved digital twinning of the equipment.
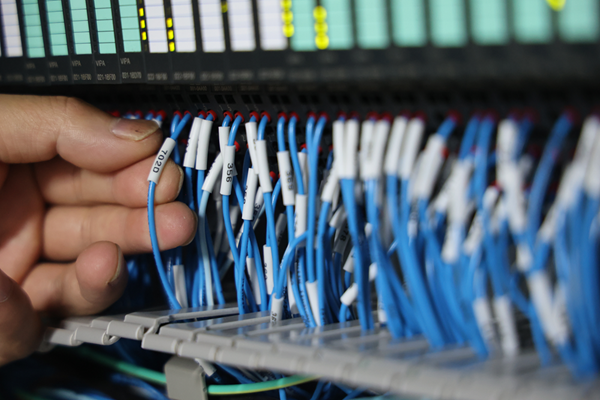
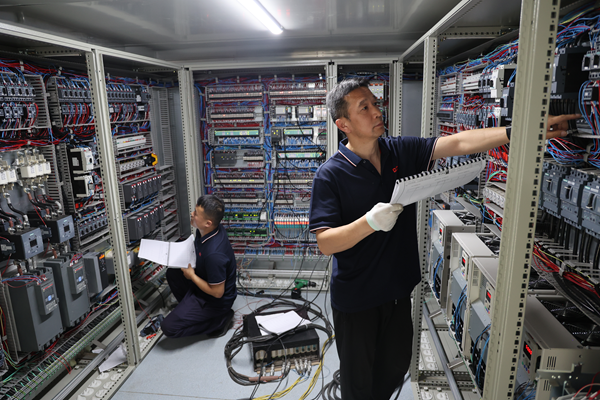
Utilizing this system, D&G Machinery's service engineers conduct remote diagnostics on customers' plant, becoming their "health consultants." No matter when and where there is a problem with the equipment, they can immediately analyze the collected data to find out the cause of the problem, and guide the operators to troubleshoot. On-site services that may have taken days or even weeks can now be solved within hours, which not only greatly improves service efficiency but also saves service expenses, achieving a win-win situation for customers and manufacturers.
D&G Machinery's asphalt mixing plant enables real-time monitoring of the voltage and current conditions of specific equipment. For example, the mixer current is an essential parameter for monitoring the working state and mixing uniformity of the mixer. By observing any abnormal current fluctuations in various components displayed on the screen, early warnings for potential equipment failures can be provided based on data analysis.
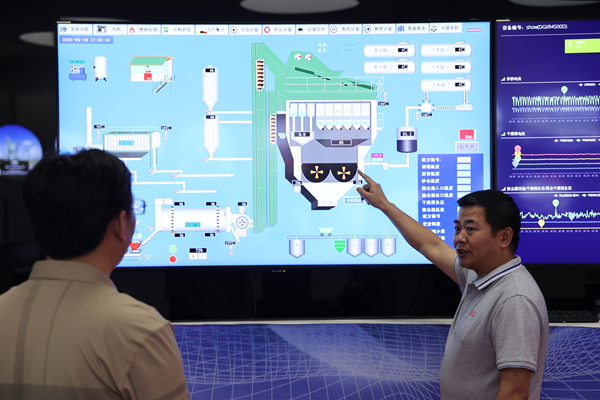
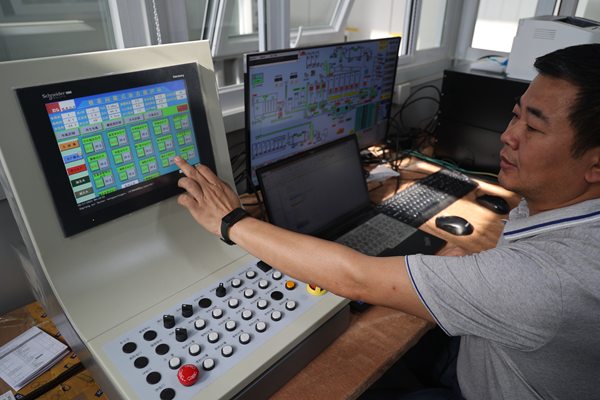
Empowered by DG Reach Service Control System, modeling and analysis of equipment status are conducted using data, giving proper maintenance and repair suggestions to customers based on the plant usage. The system can predict the replacement needs of key components and trigger timely alerts, enabling customers to precisely plan maintenance and production as per these prompts, ensuring that the equipment remains in optimal working condition. The system is not only an intelligent solution for customers; it also helps customers better utilize and maintain the plant. Meanwhile, D&G Machinery is leveraging this platform to conduct in-depth analysis of product design. The application of big data not only optimizes customer experience but also provides crucial insights for the company to improve and enhance product design.
In the era of intelligent AI digitalization, D&G Machinery's intelligent information service is becoming increasingly precise and convenient. Troubleshooting is no longer a big challenge, but heartwarming experience that remote support brings. In this age of information explosion, we leverage network connectivity to transcend geographical boundaries, enabling efficient remote technical support. D&G Machinery's intelligent information service is not only provided to equipment within the warranty period; our old customer can also receive remote support outside the warranty period.
Amid the constantly changing market environment, D&G Machinery always put user’s needs at the core, continuously optimizing product performance and improving user experience. For more details about DG Reach Service System and relevant upgrading service, please do not hesitate to contact us.